SUSTAINABILITY SPOTLIGHT | 16 SUSTAINABILITY SPOTLIGHT | 17 Because the groundwork was done by the consortium in terms of identifying technology aligned to business and sustainability needs, some impressive results are already becoming visible. The S3 Consortium have already been able to track a saving of 38 tonnes of carbon emissions though smarter processes. “As a business there are great correlations between wasted eort, wasted time and higher emissions. Tackling overproduction, stock rotation GAMIFYING processes and end-of-production waste were all key factors that led to the reduction,” says Tom. But Raynor Foods want to go much further. “This is just sustainability a starting point, and we are expecting the savings to grow through gamification. We’re aiming to be net zero by 2030, which is a deliberately ambitious target. But it’s got to be because we’re running out of time, and if Delivering worker nobody starts moving the dial quite quickly, we’re all engagement for going to be in a really unpleasant place,” says Tom. environmental impact Smart people and gamiocation The company knew that the only way to do this was to get the entire workforce on board. “Because it’s only through an engaged workforce that we’re going to deliver these things. We want to make sustainability more relevant and personal to them. One area we hope to move the needle on is making the invisible – things Raynor Foods, the 2023 British Sandwich highly innovative high-tech response linking employee One of the most impressive pieces of technology is the like CO2 emissions – visible, to motivate sta to find Association Manufacturer of the Year, and the recognition and rewards to measurable KPIs in Ultra-Wide Band Mesh, developed by Software Imaging. ways to reduce waste they can’t necessarily see,” says largest supplier of sandwiches to the NHS, sustainability performance – known as the S3 Project. It is eectively an invisible mesh that covers the entire Tom. enterprise and can locate a digital link within 5 to 10 have always been a leader in sustainability. In The aim of the S3 Project is to create a digital cm. “It is eectively the backbone of our whole project,” With the data in hand and an awareness of the changes 2009 they pioneered the carbon footprinting twin factory using state-of-the-art technology to says Tom Hollands, Innovation and Technical Director at that needed to be made, the challenge was to convey of sandwich products, and they have track carbon emissions in food manufacturing. By Raynor Foods. this information to the workforce in a way that would an extensive track record of sustainable incorporating aspects of gamification to motivate the engage them on a personal level, and to encourage the innovation delivering projects, including workforce, and real-time carbon monitoring, the aim “You can associate links with a piece of equipment, or behaviours and values that Raynor Foods want to live is to demonstrate carbon reductions. The project has to people, or to processes. And because we flooded the by as an organisation. eliminating non-biodegradable plastics and three main elements: smart people, smart processes whole area, and it’s got a very granular accuracy, you creating the IntenseTM tomato, which cut and smart factory. can do some fantastic things with the technology that To this end, they approached the IfM, part of the waste and increased product life. we’re only starting to discover now. You can add the University of Cambridge, who have been leading the Smart factory and smart processes links to scaled waste bins, which allow you to associate development of a gamification programme to make To maintain this position and push the boundaries The foundations of the S3 project have already been the amount of waste with a process. You could also add improvements in sustainability. The system, which of sustainability, Raynor Foods saw an opportunity established, with the University of Lincoln leading links to doors on room-sized fridges and freezers to allows employees to earn points that transform into a to tackle arguably their biggest challenge to date – much of the work. They analysed what improvements highlight if they are open,” says Tom. variety of rewards and benefits, is the most advanced how to motivate everyone in the company, from the were needed in terms of CO2 reduction, discovered and innovative such system in the food industry. shop floor upwards, to work towards improving its what digital tools would be needed to accomplish “These links enable you to geolocate people to a sustainability performance. To achieve this, Raynor these reductions, and were then involved in developing process. If you measure the process from a CO2e “It’s an engagement and education tool that allows Foods, in collaboration with a consortium made up of and deploying these tools. These included a highly performance perspective, you can assign performance us to motivate and achieve behavioural change, while the Institute for Manufacturing (IfM), the University sophisticated set of sensors connected to game links to individuals and teams who work in that area, even if making the work fun and valuable for the employees” of Lincoln and Software Imaging, came up with a attached to pieces of equipment or worn by employees. they only work in the area for 30 minutes.” explains Ergün Güngör, Research Associate at the IfM.
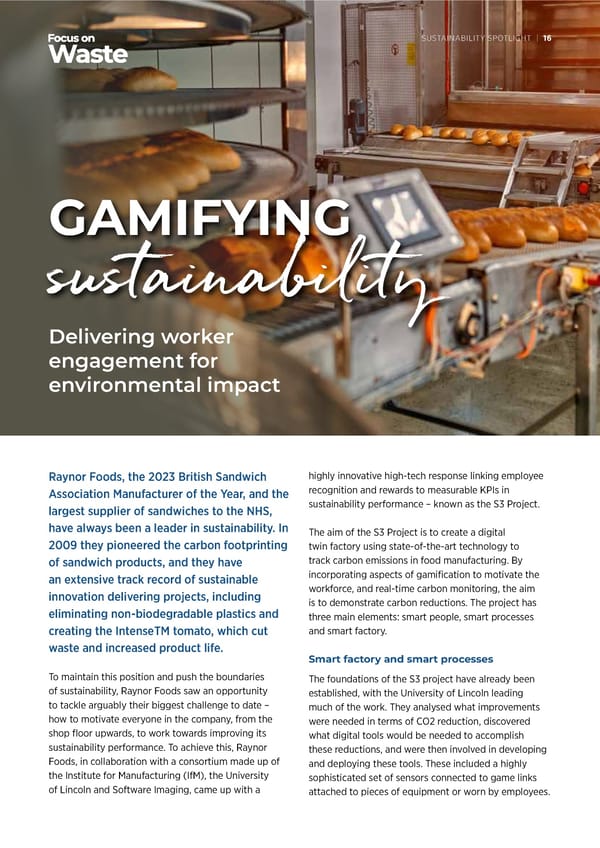